Keywords
Computer Science and Digital Science
- A5.5.1. Geometrical modeling
- A5.5.2. Rendering
- A8.3. Geometry, Topology
Other Research Topics and Application Domains
- B5.7. 3D printing
1 Team members, visitors, external collaborators
Research Scientists
- Sylvain Lefebvre [Team leader, Inria, Senior Researcher, HDR]
- Samuel Hornus [Inria, Researcher]
- Jonas Martinez Bayona [Inria, Researcher]
- Camille Schreck [Inria, from Oct 2020, Starting Faculty Position]
Faculty Member
- Cédric Zanni [Univ de Lorraine, Associate Professor]
PhD Students
- Melike Aydinlilar [Univ de Lorraine]
- Semen Efremov [Inria]
- Jimmy Etienne [CNRS]
- Marco Freire [Univ de Lorraine, from Oct 2020]
- Thibault Tricard [Univ de Lorraine]
Technical Staff
- Jean Baptiste Austruy [Univ de Lorraine, Engineer]
- Adrien Bedel [Inria, Engineer, from May 2020 until Oct 2020]
- Adrien Bedel [Inria, Engineer, from Nov 2020]
- Pierre Bedell [Univ de Lorraine, Engineer]
- Pierre Alexandre Hugron [Univ de Lorraine, Engineer]
- Yamil Salim Perchy Bocanegra [Inria, Engineer]
Interns and Apprentices
- Adrien Bedel [Inria, until Feb 2020]
- Ghilain Bergeron [Inria, from Apr 2020 until Jun 2020]
- Yoann Coudert-Osmont [École Normale Supérieure de Lyon, from Sep 2020]
Administrative Assistants
- Celine Cordier [Inria]
- Virginie Priester [CNRS]
2 Overall objectives
Digital fabrication has had a profound impact on most industries. It allows complex products to be modeled in Computer Assisted Design (CAD) software and then sent to Computer-Aided Manufacturing (CAM) devices that physically produce the products. Typical CAM devices are computer-controlled lathes and milling machines that are ubiquitous in mass-production chains, along with injection molding and assembly robots. The design of a new product requires a large pool of expertise consisting of highly skilled engineers and technicians at all stages: design, CAD modeling, fabrication, and assembly chains.
Within CAM technologies, the advent of additive manufacturing (AM) (i.e., 3D printing) together with powerful and inexpensive computational resources let us envision a different scenario. In particular, these technologies excel where traditional approaches find their limitations:
- Parts with complex geometry can be fabricated in a single production run, and the cost has no direct relationship with the geometric complexity.
- The cost-per-unit for fabricating an object is constant and significantly lower than producing a small series of objects with traditional means. Though it is not competitive on a mass-production scale where the cost-per-unit decreases as the number of produced units increases.
- The machine setup is largely independent of the object being fabricated, and thus these technologies can be made available through generic 3D printing companies and online print services. Additionally, the machines are significantly easier to operate than traditional fabrication means to the extent of making them accessible to the general public.
Consequently, it becomes possible to design and produce parts with short development cycles: physical objects are uniquely and efficiently fabricated from digital models. Each object can be personalized for a specific use or customer. The core difficulty in this context lies in modeling parts, and this remains a significant obstacle as functional, and manufacturability constraints have to be enforced. By functional constraint, we refer here to some desired behavior in terms of rigidity, weight, balance, porosity, or other physical properties. This is especially important as AM allows the fabrication of extremely complex shapes, the scales of which vary from a few microns to a few meters. All this pushes AM well beyond traditional means of production and enables the concept of metamaterials; materials where parameterized microstructures change the behavior of a base shape fabricated from a single material.
Exploiting this capability turns the modeling difficulties into acute challenges. Such a quantity of details modeling becomes intractable, and specifying the geometry with standard tools becomes a daunting task, even for experts. Besides, these details have to interact in subtle and specific ways to achieve the final functionality (e.g., flexibility, porosity) while enforcing fabrication constraints. On the process planning side (i.e., the set of computations turning the part into printing instructions), large parts filled with microstructures, porosities, and intricate multi-scale details quickly lead to huge data-sets and numerical issues.
Our overall objective is to develop novel approaches enabling experts and practitioners alike to exploit the advantages of AM fully. We aim to achieve this by developing novel algorithms that automatically synthesize or complete designs with functional details. We consider the full chain, from modeling to geometry processing, to optimize 3D printer instructions.
3 Research program
We focus on the computational aspects of shape modeling and processing for digital fabrication: dealing with shape complexity, revisiting design and customization of existing parts in view of the novel possibilities afforded by AM, and providing a stronger integration between modeling and the capabilities of the target processes.
We tackle the following challenges:
- develop novel shape synthesis and shape completion algorithms that can help users model shapes with features in the scale of microns to meters while following functional, structural, geometric, and fabrication requirements;
- propose methodologies to help expert designers describe shapes and designs that can later be customized and adapted to different use cases;
- develop novel algorithms to adapt and prepare complex designs for fabrication in a given technology, including the possibility to modify aspects of the design while preserving its functionality;
- develop novel techniques to unlock the full potential of fabrication processes, improving their versatility in terms of feasible shapes as well as their capabilities in terms of accuracy and quality of deposition;
- develop novel shape representations, data-structures, visualization, and interaction techniques to support the integration of our approaches into a single, unified software framework that covers the full chain from modeling to printing instructions;
- integrate novel capabilities enabled by advances in additive manufacturing processes and materials in the modeling and processing chains, in particular regarding the use of functional materials (e.g. piezoelectric, conductive, shrinkable).
Our approach is to cast a holistic view on the challenges above by considering modeling and fabrication as a single, unified process. Thus, the modeling techniques we seek to develop will take into account the geometric constraints imposed by the manufacturing processes (minimal thickness, overhang angles, trapped material) and the desired object functionality (rigidity, porosity). To allow for the modeling of complex shapes and adapt the same initial design to different technologies, we propose developing techniques that can automatically synthesize functional details within parts. At the same time, we will explore ways to increase the versatility of the manufacturing processes through algorithms that are capable of exploiting additional degrees of freedom (e.g., curved layering 18), can introduce new capabilities (e.g., material mixing 20) and improve part accuracy (e.g., adaptive slicing 17).
Our research program is organized along with three main research directions. The first one focuses on the automatic synthesis of shapes with intricate multi-scale geometries that conform to additive manufacturing technologies' constraints. The second direction considers geometric and algorithmic techniques for the actual fabrication of the modeled object. We aim to improve further the capabilities of the manufacturing processes with novel deposition strategies. The third direction focuses on computational design algorithms to help model parts with a gradient of properties and help customize existing designs for their reuse.
These three research directions interact strongly and cross-pollinate: e.g., novel possibilities in manufacturing unlock novel possibilities in terms of shapes that can be synthesized. Stronger synthesis methods allow for further customization.
4 Application domains
4.1 Digital Manufacturing
Our work addresses generic challenges related to fabrication and can thus be applied in a wide variety of contexts. Our aim is first and foremost to develop the algorithms that will allow variously industrial sectors to benefit more strongly from the potential of AM. To enable this, we seek collaborations with crucial industry partners developing software and AM systems for a variety of processes and materials that are of interest to specific sectors (e.g., dental, prosthetic, automotive, aerospace).
4.2 Medical Applications
To allow for faster transfer of our techniques and unlock novel applications, we actively seek to develop applications in the medical sector. In particular, we are involved in a project around the design of orthoses, which explores how our research on elasticity control through microstructure geometries can be specifically applied to the medical sector; see §9.3.
5 Highlights of the year
5.1 New results
In 2020 we made major advances on two specific problems that the team has been focusing on for several years:
- We proposed a novel approach to generate tool trajectories that result in a solid layer within a 3D print, exploiting a varying deposition width 11. This project was primarily investigated by Samuel Hornus, collaborating with Tim Kuipers (Ph.D. student at TU Delft and developer for Ultimaker) and the GAMBLE team.
- We proposed a novel type of strongly anisotropic, collapsable 3D structures that can be fabricated on low-cost filament printers. These allow for a much wider gamut of deformations, behaving like fibers in a highly flexible medium 12. This work is the last result in an overall direction of research that we started around 2015: the idea of using procedural noise patterns for structure synthesis. It is unique in the capabilities it offers, and we are hoping for wide adoption by researchers in soft robotics and material science.
5.2 Covid-19
The team helped a local effort to produce 3D printed face shields during the first confinment https://
Overall the team activity has been (and remains) significantly impacted by the pandemic, with reduced access to critical 3D printing equipment over extended periods of time.
5.3 Recruitments
The team welcomed two new members in 2020:
- Camille Schreck has been recruited on an Inria Starting Faculty Position. Camille brings her expertise of physical simulation to tackle challenges arising in computational fabrication. In particular, a reliable and efficient physical modeling of manufactured objects is necessary to optimize their design. This is an important direction of research towards the adoption by application domains of the stochastic 3D structures developed in the team.
- Marco Freire joined the team as a PhD student, exploring layout problem in computational fabrication.
5.4 Awards
The implementation of the work of Samuel Hornus et al. 11 on varying width deposition received a “replicability stamp” from ACM http://
6 New software and platforms
6.1 New software
6.1.1 IceSL
- Keyword: Additive manufacturing
- Scientific Description: IceSL is the software developed within MFX, that serves as a research platform, a showcase of our research results, a test bed for comparisons and a vector of collaborations with both academic and industry partners. The software is freely available both as a desktop (Windows/Linux) and an online version.
- Functional Description: IceSL allows users to model complex shapes through CSG boolean operations. Objects can be directly prepared and sent to a 3d printer for fabrication, without the need to compute an intermediate 3D mesh.
-
News of the Year:
In 2020 IceSL saw a number of additions to its core system, the most important was the inclusion of a plugin system.
As of now, this plugin architecture allows external collaborators to do three main things, (a) create their own deposition strategy to fill 3d printed objects, (b) export the results of the slicing engine to any machine code and (c) perform multiple post-processing stages on the slicing output of IceSL. Flexibility and complete integration are guaranteed and examples of all three cases are also present in this addition. Currently, IceSL uses this system to include an implementation of a fill technique authored by the group 11 in the form of a plugin.
A central piece of IceSL’s feedback to the user, called the “G-code preview”, was reworked and vastly improved. This previewer creates a visual representation of the expected printed output that is helpful to the user in making informed decisions before printing and by extension spending raw material. Multiple small additions, fixes and improvements were done to increase user flexibility, stability, accuracy of results and compatibility with multiple platforms. All of the above, with the exception of plugins were also included in the online version.
There were eight beta releases and one stable in 2020, with around 90K total downloads (6.5K of latest). In addition the online version of IceSL, Slicecrafter, is processing around 75 models per day (15K total this year).
-
URL:
https://
icesl. loria. fr - Authors: Sylvain Lefebvre, Frédéric Claux, Jonas Martinez-Bayona, Jean Hergel, Jérémie Dumas, Samuel Hornus, Yamil Salim Perchy, Cédric Zanni, Pierre Bedell
- Contacts: Sylvain Lefebvre, Jean-Philippe Schaeffer
- Participants: Frédéric Claux, Jean Hergel, Jérémie Dumas, Jonas Martinez-Bayona, Samuel Hornus, Sylvain Lefebvre, Pierre Bedell, Cédric Zanni, Noemie Vennin, Thibault Tricard, Jimmy Etienne, Yamil Salim Perchy, Pierre-Alexandre Hugron
6.1.2 IceSL WebPrinter
- Name: IceSL Web3DPrinter
- Keyword: 3D printing
- Functional Description: In Web3DPrinter, a user can input (either by loading it or by copy-pasting it) a Gcode destined to any 3D printer. The tool will then parse the Gcode and produce a visual simulation of it. The loaded Gcode can also be browsed and modified in the attached text editor, allowing to see in real time the impact of such modification. Following the last feature, the tool can provide an easy-to-use setup for educational purposes.
- Release Contributions: -
- News of the Year: Web3DPrinter (VrPrinter initially) started as an internal project to help us visualize specific Gcodes and to help with teaching. We have started to update it with the aim to release it publicly. At first available on its own website on November 2020, our goal is to further integrate it within the IceSL’s website and communicate about it in 2021.
- Authors: Pierre Bedell, Yamil Salim Perchy, Sylvain Lefebvre
- Contact: Sylvain Lefebvre
6.1.3 Silice
- Name: Silice
- Keywords: FPGA, Programming
- Functional Description: Silice makes it possible to write algorithms for FPGAs in the same way we write them for processors: defining sequences of operations, subroutines that can be called, and using control flow statements such as while and break. At the same time, Silice lets you fully exploit the parallelism and niceties of FPGA architectures, describing operations and algorithms that run in parallel and are always active, as well as pipelines. Silice remains close to the hardware: nothing gets obfuscated away. When writing an algorithm you are in control of what happens at which clock cycle, with predictable rules for flow control. Clock domains are exposed. In fact, Silice compiles to and inter-operates with Verilog: you can directly instantiate and bind with existing modules.
- Release Contributions: Initial release.
- News of the Year: Sylvain Lefebvre is continuing work on Silice, exploring the use of FPGA architectures for high performance Graphics and Geometry processing. Silice and its demos (the Doom-chip in particular) have been featured on several websites in 2020: hackernews, engadget, vice.com.
-
URL:
https://
github. com/ sylefeb/ Silice - Author: Sylvain Lefebvre
- Contact: Sylvain Lefebvre
6.2 New platforms
Participants: Pierre Bedell, Pierre-Alexandre Hugron.
We continued our active participation within the Creativ'Lab, a common experimental platform funded by Inria, Loria, CNRS and Région Grand Est.
We added a large FDM 3D printer, that allows us to work on life-sized models. Alongside this large printer, we also acquired a small DLP resin printer to start exploring new problems related to these technologies.
We did a complete reorganization of this space by moving all our machines there, thus creating an unique space to conduct our experiments.
With the Orthosis 4D project growing, we setted up a small print farm with custom machines specialized into printing flexible filament, and a dehydrator to help us restoring properties of this special material.
As the Creativ'Lab will expand its scope, an additional printing room is projected. This new room will be dedicated to resin printing. This extension will give us the possibility to setup our future large format resin printer, which will be a powerful asset in our explorations of the resin technologies. This new printing room will also host the 3D printers of the LARSEN team, creating a collaborative space around resin printing.
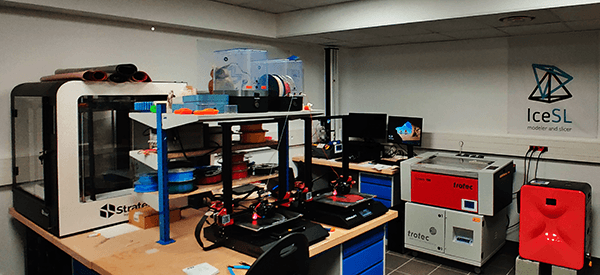
7 New results
7.1 Variable-width contouring for additive manufacturing
Participants: Samuel Hornus, Tim Kuipers, Olivier Devillers, Jonàs Martínez, Monique Teillaud, Marc Glisse, Sylvain Lazard, Sylvain Lefebvre.
This work stems from the observation that the FDM fabrication process leaves a
lot of porosities (small holes, abstractly referred to as underfill) in
areas that are requested to be completely covered with the matter.
This is because the extrusion tool can not move back to areas where it has
already deposited matter, for such a collision might disrupt the quality of the
printed slice or even dislodge the printed object from its base (ruining the
whole print).
Having observed that it is possible to vary the deposition width along
a deposition path slightly, we set out to leverage the freedom to minimize underfill.
The problem of underfill minimization has, to our knowledge, never been
attacked as directly as we have, but it appears important to maximize the
mechanical strength of the printed piece.
Our novel technique decomposes a planar shape (the future solid slice) into
ribbons of varying width that gradually evolve into circular shapes that are
easier to handle.
Some results of our technique can be examined at
https://
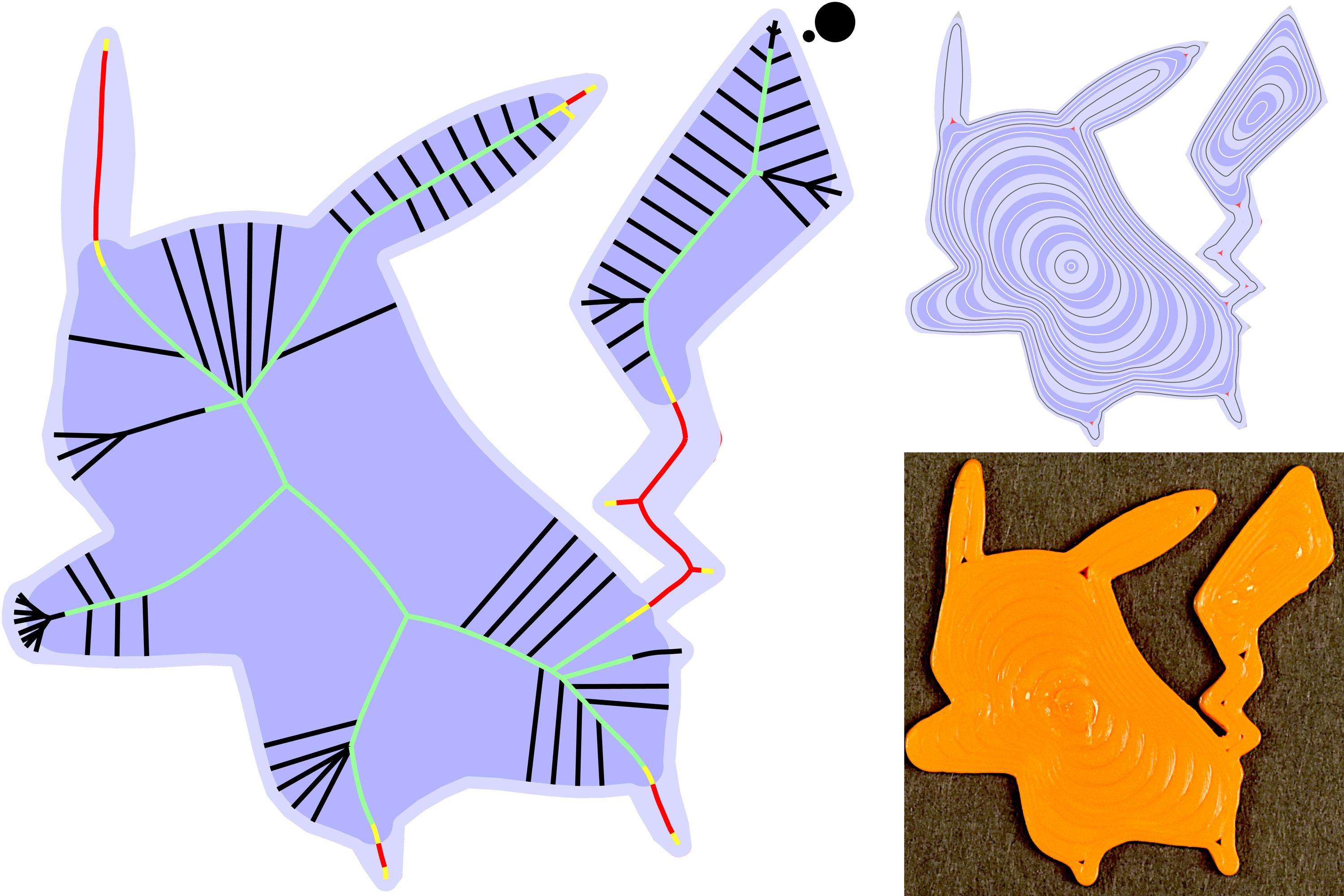
7.2 Freely orientable microstructures for designing deformable 3D prints
Participants: Thibault Tricard, Vincent Tavernier, Cédric Zanni, Jonàs Martínez, Pierre-Alexandre Hugron, Fabrice Neyret, Sylvain Lefebvre.
In this work, we explore novel small-scale structures for 3D printing. Our structures' originality is that they produce a fiber-like mechanical response, with a single rigid direction (along the fibers) and two transversal highly flexible directions. The structures – and their mechanical response – can be freely spatially graded in orientation and density. This allows the control of the way the volume reshapes when deformed and results in a wide range of design possibilities.
We base our technique on the procedural phasor noise, using its procedural nature to extract these structures in a very efficient manner. We study the structures from a signal point of view and propose ways to reduce significantly the number of singularities (local degeneracies) generated by the procedural phasor noise. This improves the mechanical compliance of the generated structures.
This article was published in Transaction on Graphics 12 in November 2020 and virtually presented at SIGGRAPH Asia by Thibault Tricard in December 2020.
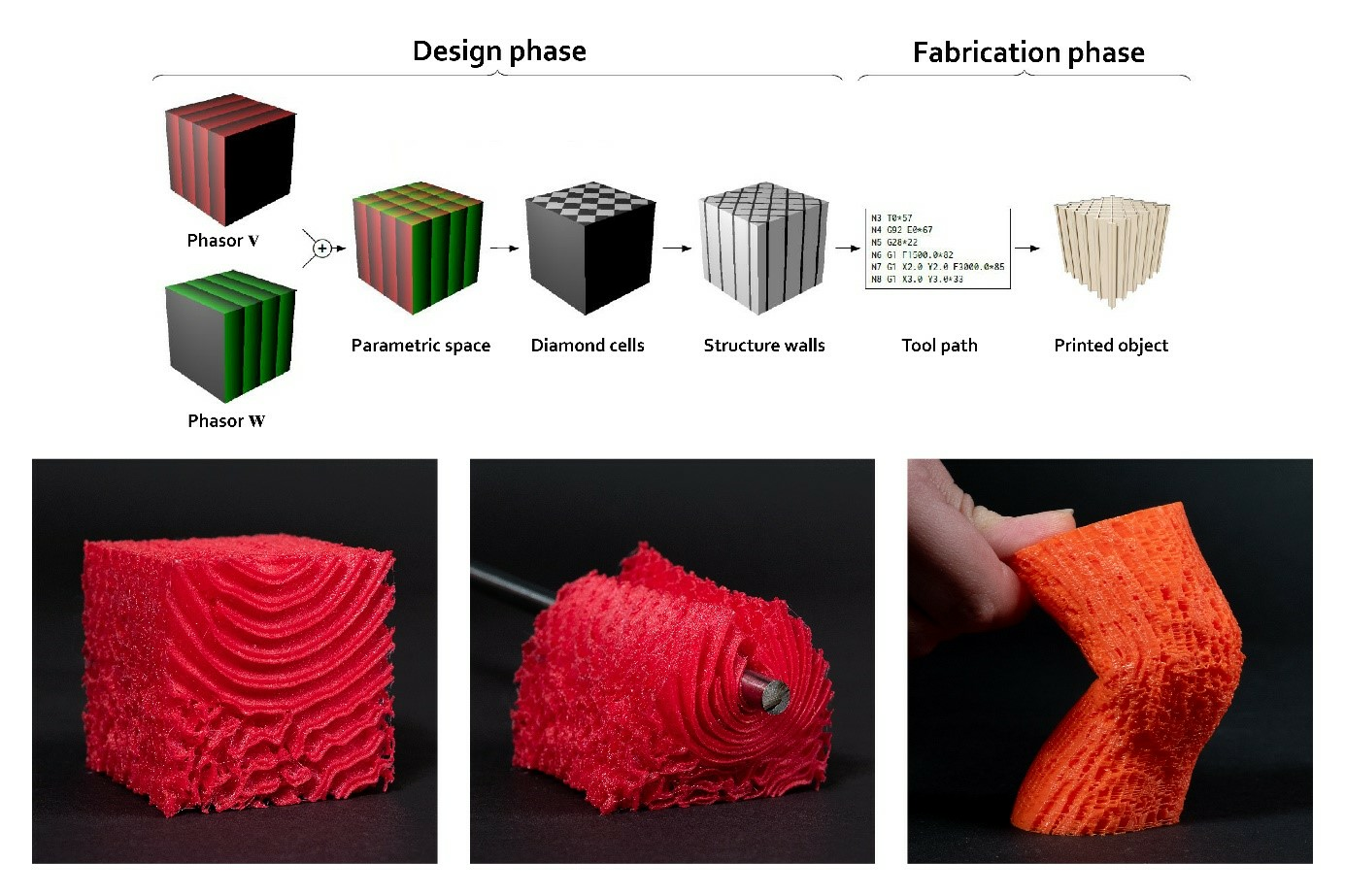
7.3 Anisotropic soft robots based on 3D printed meso-structured materials: design, modeling by homogenization and simulation
Participants: Félix Vanneste, Olivier Goury, Jonàs Martínez, Sylvain Lefebvre, Hervé Delingette, Christian Duriez.
In this project, led by our colleagues from team DEFROST (Inria Lille), we explored using 3D-printed mesostructured materials to build soft robots and presented a modeling pipeline for design assistance and control 13. These meta-materials can be programmed before printing to target specific mechanical properties, remarkably heterogeneous stiffness, and anisotropic behavior. Without changing the external shape, the meta-materials lead to a dramatic change in the kinematics of the robot (see Figure 4). This highlights the importance of modeling. Therefore, to help design and control soft robots made of these mesostructured materials, a modeling method is introduced. It relies on numerical homogenization and the Finite Element Method (FEM) to capture the anisotropic deformations of the interal microstructures. This work is a great example of how the meta-meterials developped within MFX can lead to further research in other domains, here soft-robotics.
A video showcase can be found at https://
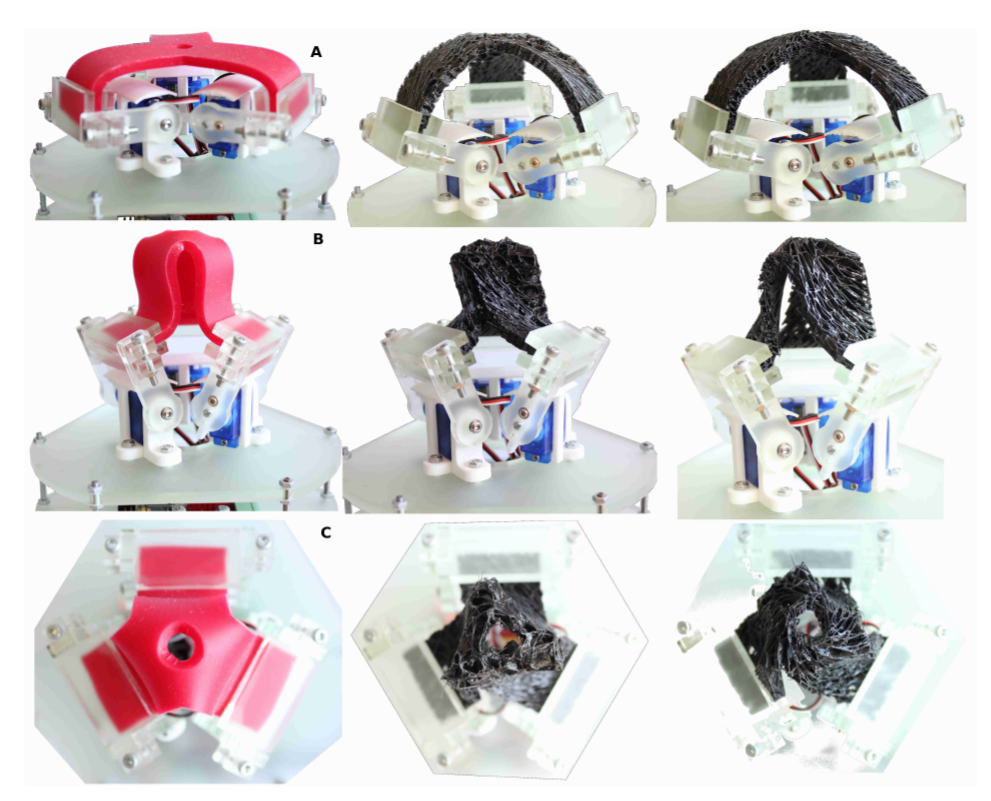
7.4 Fast ray tracing of scale-invariant integral surfaces
Participants: Melike Aydinlilar, Cédric Zanni.
Scale-invariant integral surfaces, which are implicit representations of surfaces, provide a way to define smooth surfaces from skeletons with prescribed radii defined at their vertices. They can be used to represent a large range of shapes, from procedural foam structures to truss structures and artistic shapes (see Figure 5). We introduce a new rendering pipeline allowing us to visualize such surfaces in real-time. The proposed method relies on combining a new field normalization, a ray segmentation based on the distance to primitives, and iterative polynomial approximations. Our GPU implementation uses a dynamic data-structure to provide constant-time access to primitive during ray processing. A paper has been submitted to Computer Graphic Forum. The implementation is done in an internal version of IceSL.
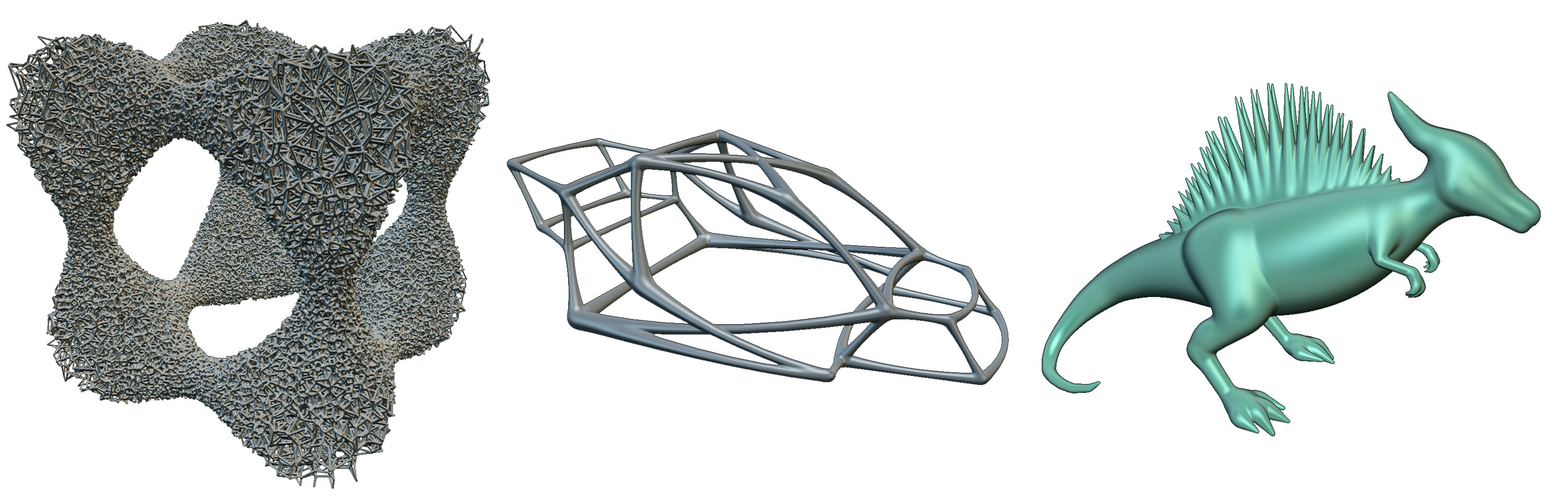
7.5 Procedural band patterns
Participants: Jimmy Etienne, Sylvain Lefebvre.
In the past years, we have studied ways to quickly generate complex infill patterns that can adapt to target density changes. One way to achieve this is to generate families of curves that are evenly spaced, locally parallel, but where the spacing changes according to a scaling field.We propose a novel algorithm that generates such line patterns. It allows for progressive scale gradations, avoiding the abrupt doubling of the number of lines of typical subdivision approaches. Each band – space in between two lines – is uniquely identified by an integer number, allowing for a wide range of effects. This technique finds applications for texturing, and of course, for our initial goal of producing infill patterns as illustrated in Figure 6. It is integrated into our software IceSL. The work was published at I3D 2020 15 and presented by Jimmy Etienne at the virtual conference.
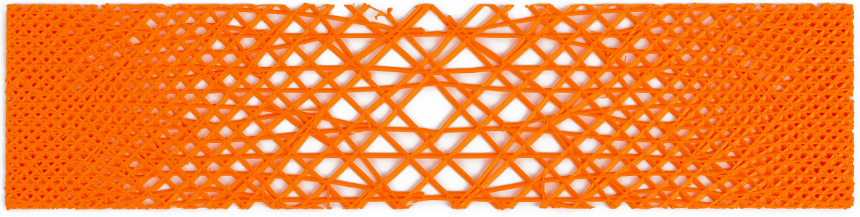
8 Bilateral contracts and grants with industry
8.1 Bilateral contracts with industry
Partnership with AddUp
- Company: AddUp.
- Duration: Started in 2019.
- Participants: Sylvain Lefebvre.
- Abstract:
AddUp (https://
www. ) is a French manufacturer of metal 3D printers for high-end industrial applications. We announced during FormNext 2019 (November) a partnership towards the creation of new software technologies. This partnership continued to develop in 2020 with several new advances.addupsolutions. com/ en/
9 Partnerships and cooperations
9.1 International initiatives
9.1.1 Inria international partners
Informal international partners
We had collaborations with several international partners in 2020:
- Samuel Hornus worked jointly with Tim Kuipers from TU Delft/Ultimaker in the context of the varying deposition project 11.
- Sylvain Lefebvre worked jointly with co-authors from University of New York, University of British Columbia and CNR ISTI on a method for fabricating objects by milling 14.
- We have an ongoing project on infill trajectories with Sue Whitesides and Nishat Rahnuma Islam from the University of Victoria in British Columbia.
9.2 National initiatives
9.2.1 ANR
Project MuFFin
- Acronym: MuFFin.
- Title: Procedural Stochastic Microstructures for Functional Fabrication.
- Duration: 2018-2021.
- Funding: ANR JCJC.
- Coordinator: Jonàs Martínez.
- Participants: Jonàs Martínez, Sylvain Lefebvre, Samuel Hornus, Semyon Efremov.
-
Abstract:
MuFFin aims at contributing a unified pipeline for the efficient and scalable synthesis, visualization, and modeling of additively manufactured microstructures with tailored macroscopic physical behavior. In an interdisciplinary effort, MuFFin will blend computer and material science perspectives to deliver an integrated approach that is both computationally and physically sound.
As a highlight, this year, we have submitted for publication an article that proposes a method to efficiently generate random auxetic 2D materials 16. Currently, Semyon Efremov is also leading research on the extension of 19 to the three-dimensional case, which is far more complex.
Project IMPRIMA
- Acronym: IMPRIMA.
- Title: Implicit modeling for additive manufacturing.
- Duration: 2019-2023.
- Funding: ANR JCJC.
- Coordinator: Cédric Zanni.
- Participants: Cédric Zanni, Sylvain Lefebvre, Melike Aydinlilar, Nathaniel Seyler.
-
Abstract:
Project IMPRIMA seeks to explore novel implicit representations to provide a unified approach for the modeling and slicing of both macro geometry, microstructures, and gradient of material. Additionally, this research aims to complete tight integration of both standard boundary representations and novel implicit volume representations, allowing the best choice of representation for different parts of a design.
Our latest results on the visualization of scale-invariant integral surfaces (SCALIS), a surface representation suited for the description of both micro and macro geometry, has been accepted for publication in the Computer Graphics Forum journal, to appear in 2021. We have hired Nathaniel Seyler as an Engineer, starting from January 2020. Currently, Melike Aydinlilar is working on the extension of the proposed method to the slicing of the SCALIS representation.
9.3 Regional initiatives
Project Orthosis4D
- Acronym: Orthosis4D.
- Title: Passive and active 3D printed orthosis: modeling, simulation and applications.
- Duration: 2019-2022.
- Funding: Lorraine Université d’Excellence.
- Coordinator: Sylvain Lefebvre.
- Participants: Sylvain Lefebvre, Thibault Tricard, Pierre-Alexandre Hugron, Jean-Baptiste Austruy
- Other partners: IJL, LRGP, ERPI, IRR and Nancy CHU
-
Abstract:
The project considers the creation of flexible plates with controlled elasticity for use in medical applications (orthoses, insoles). It exemplifies our approach of doing focused collaborations around application domains of our research, to ensure that our techniques answer actual practical challenges and maximize the chances that they are deployed in the near future. On our side the project funds a PhD student, Thibault Tricard, who started in October 2018, a project manager, Jean-Baptiste Austruy, who started in May 2019 and a design engineer, Pierre-Alexandre Hugron, who started in April 2019.
In 2020, we proposed a novel type of microstructure, studied primarily by Thibault Tricard 12. This novel type of structures is being used within the evaluation of 3D printed insoles, alongside other structures developped within MFX in the past years.
Pierre-Alexandre Hugron 3D printed more than 180 pairs of insoles – improving the reliability, accuracy and speed of the 3D printing process with flexible filaments. These insoles will be used for clinical tests in collaboration with Edem Alado (CHRU Nancy), hopefully in 2021 (depending on the pandemic situation). Pierre-Alexandre Hugron also worked jointly with Institut Jean Lamour (Samuel Kenzari & Thomas Hauet) on the topic of measuring orthosis deformations.
10 Dissemination
10.1 Promoting scientific activities
Member of the conference program committees
- Jonàs Martínez was on the full papers program committee of EUROGRAPHICS 2021.
- Jonàs Martínez was an associate editor of 2020 IEEE/RSJ International Conference on Intelligent Robots and Systems.
- Cédric Zanni was on the full papers program committee of SMI 2020.
- Samuel Hornus was on the program committee for GRAPP 2021.
- Sylvain Lefebvre was on the program committee of SIGGRAPH Asia 2020, SMI 2020, and was Conflict of Interest Coordinator for SIGGRAPH 2020. He was on the Advisory Board of the EUROGRAPHICS 2020 conference.
Reviewer
- Jonàs Martínez was a reviewer for SIGGRAPH 2020 and SIGGRAPH Asia 2020.
- Cédric Zanni was a reviewer for JFIG 2020.
- Samuel Hornus was a reviewer for SIGGRAPH 2020, GRAPP 2021.
- Sylvain Lefebvre was a reviewer for SMI 2020, SIGGRAPH 2020, SIGGRAPH Asia 2020.
- Thibault Tricard was a reviewer for Pacific Graphics 2020 and Eurographics 2021.
10.1.1 Journal
Reviewer - reviewing activities
- Jonàs Martínez was a reviewer of ACM Transactions on Graphics, Graphical Models, Computer-Aided Design, Computers & Graphics, and PLOS ONE.
- Cédric Zanni was a reviewer of Graphical Models.
- Samuel Hornus was a reviewer of ACM Transactions on Graphics.
- Sylvain Lefebvre was a reviewer for ACM Transactions on Graphics, IEEE Transactions on Visualization, and Computer & Graphics.
10.1.2 Invited talks
- Sylvain Lefebvre gave a keynote at SPM 2020 (virtual conference), was invited at the CECAM EPFL Workshop on Computing Complex Mechanical Systems (22-24/01/2020) where he gave a presentation (https://
www. ), gave a (virtual) invited talk at the University of Hasselt (Belgium), and an invited presentation at the (virtual) symposium Impression 3D des polymères hosted by Ecole Polytechnique.cecam. org/ workshop-details/ 76/ - Jonàs Martínez gave a virtual talk at Forum Cyberdéfense & Stratégie 2020 (France).
10.1.3 Research administration
- Jonàs Martínez is the scientific correspondent for Europe (Inria Nancy Grand-Est).
- Jonàs Martínez was member of the jury for the 2020 CRCN competition at Inria Nancy Grand-Est.
- Samuel Hornus was animating the local “Comité du Développement Technologique” until august 2020.
- Sylvain Lefebvre is animating the local “Comité du Développement Technologique” since september 2020.
- Sylvain Lefebvre is co-organizing the 'TutoTechno' with Bertrand Wallrich and Monique Teillaud, a series of tutorial events on emerging technologies within the Inria Nancy Grand-Est center.
10.2 Teaching - Supervision - Juries
10.2.1 Teaching
- Master : Jonàs Martínez, Introduction to data parallelism, 18h ETD, Université de Lorraine, France.
- Master : Jonàs Martínez, Geometric modeling for additive manufacturing, 10h ETD, ENSEM Nancy, France.
- Master: Cédric Zanni, Software Engineering, 24.5h ETD, M1, École des Mines de Nancy, France.
- Master: Cédric Zanni, Operating System, 12h ETD, M1, École des Mines de Nancy, France.
- Master: Cédric Zanni, Introduction to C/C++, 21h ETD, M1, École des Mines de Nancy, France.
- Master: Cédric Zanni, Techniques for video game programming, 18h ETD, M1, École des Mines de Nancy, France.
- Master: Cédric Zanni, ARTEM Game Lab, 12h ETD, M1, École des Mines de Nancy, France.
- Master: Sylvain Lefebvre, Additive manufacturing for soft robotics, 6h ETD, École Polytechnique, Saclay, France.
- Master: Sylvain Lefebvre, Introduction to parallel programming, 9h ETD, ENSG Nancy, France.
- Master: Sylvain Lefebvre, Introduction to additive manufacturing, 9h ETD, ENSEM Nancy, France.
- IUT: Sylvain Lefebvre, Modeling with IceSL, 12h ETD, IUT Charlemagne (Nancy), France.
- Formation continue: Sylvain Lefebvre, Modeling with IceSL, 6h ETD, OpenEdge (Dieuze), France.
- License : Cédric Zanni, Computer science, 11h ETD, École des Mines de Nancy, France.
- License : Cédric Zanni, Introduction to Computer Science, 6h ETD, École des Mines de Nancy, France.
- License : Samuel Hornus, Mathematics for Computer Science, 32h ETD, Télécom Nancy, France. (responsible of class series for 2019-2020.)
- Master: Thibault Tricard, ARTEM Game Lab, 24h ETD, M1, École des Mines de Nancy, France.
- Master: Thibault Tricard, Introduction to data parallelism, 12h ETD, Université de Lorraine, France.
- IUT: Jimmy Étienne, Introduction to programming, 56h ETD, IUT Charlemagne (Nancy), France.
- IUT: Jimmy Étienne, Second year project supervision, 8h, IUT Charlemagne (Nancy), France.
10.2.2 Supervision
- PhD in progress : Marco Freire, Layout problems in Computer Graphics and beyond, started October 2020, advisors: Sylvain Lefebvre, Samuel Hornus.
- PhD in progress : Thibault Tricard, Procedural synthesis of structured patterns, started October 2018, advisors: Sylvain Lefebvre, Dider Rouxel (IJL).
- PhD in progress : Jimmy Étienne, Curved slicing for additive manufacturing, started September 2018, advisors: Sylvain Lefebvre, Cédric Zanni
- PhD in progress : Semyon Efremov, procedural microstructures for additive manufacturing, started October 2018, advisors: Jonàs Martínez, Sylvain Lefebvre
- PhD in progress : Melike Aydinlilar, Implicit modeling for additive manufacturing, started November 2019, advisors: Cédric Zanni, Sylvain Lefebvre.
10.2.3 Juries
Sylvain Lefebvre was a reviewer (rapporteur) on the Ph.D. thesis of Thomas Buffet (University of Strasbourg) and participated in the mid-term thesis committees of Nicolas Lutz and Pascal Guehl (University of Strasbourg). He was a reviewer (rapporteur) on the Habilitation defense of Guillaume Gilet (University of Limoges). He was a member of the Ph.D. jury of Adam Gaier (Lorraine University), and a commitee member on the Ph.D. jury of Ran Zhang (IST Austria).
Sylvain Lefebvre was a member of the jury for the Young Researcher Fellow EGFR, which awards every year a young French researcher with outstanding research and community contributions in Computer Graphics.
Cédric Zanni was a jury member for the Ph.D. defense of Thomas Buffet (Ecole polytechnique).
10.3 Popularization
Beyond the team website, we maintain an online activity towards a general audience, in particular on the IceSL forum (200 members) and IceSL twitter account (@iceslapp, 500 followers).
11 Scientific production
11.1 Major publications
- 1 articleOptimal discrete slicingACM Transactions on Graphics361February 2017, 1 - 16
- 2 articleBridging the Gap: Automated Steady Scaffoldings for 3D PrintingACM Transactions on Graphics334July 2014, 98:1 - 98:10
- 3 article Variable-width contouring for additive manufacturing ACM Transactions on Graphics 39 4 (Proc. SIGGRAPH) July 2020
- 4 article By-example synthesis of structurally sound patterns ACM Transactions on Graphics 2015
- 5 articleProcedural Voronoi Foams for Additive ManufacturingACM Transactions on Graphics352016, 1 - 12
- 6 articleStructure and appearance optimization for controllable shape designACM Transactions on Graphics346November 2015, 12
- 7 articlePolyhedral Voronoi diagrams for additive manufacturingACM Transactions on Graphics374August 2018, 15
- 8 articleOrthotropic k-nearest foams for additive manufacturingACM Transactions on Graphics364July 2017, 121:1--121:12
- 9 article Freely orientable microstructures for designing deformable 3D prints ACM Transactions on Graphics December 2020
11.2 Publications of the year
International journals
- 10 article 3D Geological Image Synthesis From 2D Examples Using Generative Adversarial Networks Frontiers in Water 2 October 2020
- 11 article Variable-width contouring for additive manufacturing ACM Transactions on Graphics 39 4 (Proc. SIGGRAPH) July 2020
- 12 article Freely orientable microstructures for designing deformable 3D prints ACM Transactions on Graphics December 2020
- 13 articleAnisotropic soft robots based on 3D printed meso-structured materials: design, modeling by homogenization and simulationIEEE Robotics and Automation Letters52January 2020, 2380-2386
- 14 article DHFSlicer: Double Height-Field Slicing for Milling Fixed-Height Materials ACM Transactions on Graphics 39 6 November 2020
Conferences without proceedings
- 15 inproceedingsProcedural band patternsSymposium on Interactive 3D Graphics and GamesSymposium on Interactive 3D Graphics and GamesSan Francisco, United Stateshttps://dl.acm.org/doi/10.1145/3384382.3384522May 2020, 1 - 7
Reports & preprints
- 16 misc Random Auxetic Porous Materials from Parametric Growth Processes November 2020
11.3 Cited publications
- 17 articleOptimal discrete slicingACM Transactions on Graphics361February 2017, 1 - 16
- 18 articleSupport-free volume printing by multi-axis motionACM Transactions on Graphics374July 2018, 1 - 14
- 19 articleStar-Shaped Metrics for Mechanical Metamaterial DesignACM Transactions on Graphics384Special issue, SIGGRAPH 2019July 2019, Article No. 82 :1-13
- 20 unpublishedColored fused filament fabricationDecember 2017, working paper or preprint