2024Activity reportProject-TeamMFX
RNSR: 201822795D- Research center Inria Centre at Université de Lorraine
- In partnership with:Université de Lorraine
- Team name: Matter from Graphics
- In collaboration with:Laboratoire lorrain de recherche en informatique et ses applications (LORIA)
- Domain:Perception, Cognition and Interaction
- Theme:Interaction and visualization
Keywords
Computer Science and Digital Science
- A5.5.1. Geometrical modeling
- A5.5.2. Rendering
- A8.3. Geometry, Topology
Other Research Topics and Application Domains
- B5.7. 3D printing
1 Team members, visitors, external collaborators
Research Scientists
- Sylvain Lefebvre [Team leader, INRIA, Senior Researcher]
- Xavier Chermain [INRIA, ISFP]
- Jonas Martinez Bayona [INRIA, Researcher]
- Camille Schreck [INRIA, ISFP]
Faculty Member
- Cedric Zanni [UL, Associate Professor]
Post-Doctoral Fellows
- Eric Garner [INRIA, Post-Doctoral Fellow, from Jun 2024]
- Charline Grenier [UL, Post-Doctoral Fellow, from Dec 2024]
- David Jourdan [INRIA, Post-Doctoral Fellow, until May 2024]
- Rebekka Vaarum Woldseth [INRIA, Post-Doctoral Fellow, from Sep 2024]
PhD Students
- Giovanni Cocco [INRIA, from Dec 2024]
- Marco Freire [UL, ATER, from Oct 2024]
- Marco Freire [Inria, from Apr 2024 until Sep 2024]
- Marco Freire [INRIA, until Mar 2024]
- Luis Mollericon Titirico [INRIA]
Technical Staff
- Vincent Belle [INRIA, Engineer, from Nov 2024]
- Pierre-Alexandre Hugron [INRIA, Engineer]
- Lucas Ochocinski [INRIA, Engineer, from Nov 2024]
- Yamil Salim Perchy Bocanegra [INRIA, Engineer]
Interns and Apprentices
- Camille Charron [INRIA, Intern, from Jun 2024 until Aug 2024]
- Giovanni Cocco [Université de Milan, from Mar 2024 until Aug 2024]
- Alois Lemaux [UL, Intern, from Oct 2024]
- Antoine Marion [UL, Intern, from May 2024 until Jun 2024]
- Yan Rabefaniraka [UL, Intern, from May 2024 until Jun 2024]
- Antoine Ritter [INRIA, Intern, until Apr 2024]
Administrative Assistants
- Nathalie Bethus [CNRS, from Mar 2024]
- Juline Brevillet [UL, until Nov 2024]
- Antoinette Courrier [CNRS]
- Sylvie Hilbert [CNRS]
- Cecilia Olivier [INRIA]
Visiting Scientist
- Emilio Ottonello [IIT, Italia, until Mar 2024]
2 Overall objectives
Digital fabrication has had a profound impact on most industries. It allows complex products to be modeled in Computer Assisted Design (CAD) software and then sent to Computer-Aided Manufacturing (CAM) devices that physically produce the products. Typical CAM devices are computer-controlled lathes and milling machines that are ubiquitous in mass-production chains, along with injection molding and assembly robots. The design of a new product requires a large pool of expertise consisting of highly skilled engineers and technicians at all stages: design, CAD modeling, fabrication, and assembly chains.
With CAM technologies, the advent of Additive Manufacturing (AM) (i.e., 3D printing) and powerful and inexpensive computational resources let us envision a different scenario. In particular, these technologies excel where traditional approaches find their limitations:
- Parts with complex geometry can be fabricated in a single production run, and in most situations, the cost is not significantly impacted by the geometric complexity.
- The cost-per-unit for fabricating an object is constant and significantly lower than producing a small series of objects with traditional means. However, it is not competitive on a mass-production scale where the cost-per-unit decreases as the number of produced units increases.
- The machine setup is largely independent of the object being fabricated, and thus, these technologies can be made available through generic 3D printing companies and online print services. Additionally, the machines are significantly easier to operate than traditional fabrication means. This makes them accessible to the general public and well-suited for rapid design iterations and prototyping.
Consequently, designing and producing parts with short development cycles becomes possible: physical objects are uniquely and efficiently fabricated from digital models. Each object can be personalized for a specific use or customer. The core difficulty in this context lies in modeling parts, and this remains a significant obstacle as functional and manufacturability constraints have to be enforced. By functional constraint, we refer here to some desired behavior in terms of rigidity, weight, balance, porosity, or other physical properties. This is especially important as AM allows the fabrication of extremely complex shapes, the scales of which vary from a few microns to a few meters. All this pushes AM well beyond traditional means of production and enables the concept of metamaterials; materials where parameterized microstructures change the behavior of a base shape fabricated from a single material.
Exploiting this capability turns the modeling difficulties into acute challenges. Such quantity of details modeling becomes intractable, and specifying the geometry with standard tools becomes daunting, even for experts. Besides, these details have to interact in subtle and specific ways to achieve the final functionality (e.g., flexibility, porosity) while enforcing fabrication constraints. On the process planning side (i.e., the set of computations turning the part into printing instructions), large parts filled with microstructures, porosities, and intricate multi-scale details quickly lead to huge data sets and numerical issues.
We aim to develop novel approaches enabling experts and practitioners to exploit AM's advantages fully. We aim to achieve this by developing novel algorithms automatically synthesizing or completing designs with functional details. We consider the entire chain, from modeling to geometry processing, to optimize 3D printer instructions.
3 Research program
We focus on the computational aspects of shape modeling and processing for digital fabrication: dealing with shape complexity, revisiting design and customization of existing parts given the novel possibilities afforded by AM, and providing a stronger integration between modeling and the capabilities of the target processes.
We tackle the following challenges:
- develop novel shape synthesis and shape completion algorithms that can help users model shapes with features in the scale of microns to meters while following functional, structural, geometric, and fabrication requirements;
- propose methodologies to help expert designers describe shapes and designs that can later be customized and adapted to different use cases;
- develop novel algorithms to adapt and prepare complex designs for fabrication in a given technology, including the possibility to modify aspects of the design while preserving its functionality;
- develop novel techniques to unlock the full potential of fabrication processes, improving their versatility in terms of feasible shapes as well as their capabilities in terms of accuracy and quality of deposition;
- develop novel shape representations, data-structures, visualization, and interaction techniques to support the integration of our approaches into a single, unified software framework that covers the full chain from modeling to printing instructions;
- integrate novel capabilities enabled by advances in additive manufacturing processes and materials in the modeling and processing chains, in particular regarding the use of functional materials (e.g., piezoelectric, conductive, shrinkable).
Our approach is to cast a holistic view on the challenges above by considering modeling and fabrication as a single, unified process. Thus, the modeling techniques we seek to develop will consider the geometric constraints imposed by the manufacturing processes (minimal thickness, overhang angles, trapped material) and the desired object functionality (rigidity, porosity). To allow for the modeling of complex shapes and adapt the same initial design to different technologies, we propose developing techniques that can automatically synthesize functional details within parts. At the same time, we will explore ways to increase the manufacturing processes' versatility through algorithms capable of exploiting additional degrees of freedom, introducing new capabilities, and improving part accuracy.
Our research program is organized along with three main research directions. The first focuses on the automatic synthesis of shapes with intricate multi-scale geometries conforming to the constraints of additive manufacturing technologies. The second direction considers geometric and algorithmic techniques for the actual fabrication of the modeled object. We aim to further improve the manufacturing processes' capabilities with novel deposition strategies. The third direction focuses on computational design algorithms to help model parts with a gradient of properties and help customize existing designs for their reuse.
These three research directions interact strongly and cross-pollinate: e.g., novel possibilities in manufacturing unlock novel possibilities in terms of shapes that can be synthesized. Stronger synthesis methods allow for further customization.
4 Application domains
4.1 Digital Manufacturing
Our work addresses generic challenges related to fabrication and can thus be applied in a wide variety of contexts. Our aim is first and foremost to develop the algorithms that will allow variously industrial sectors to benefit more strongly from the potential of AM. To enable this, we seek collaborations with crucial industry partners developing software and AM systems for a variety of processes and materials that are of interest to specific sectors (e.g., dental, prosthetic, automotive, aerospace).
4.2 Medical Applications
To allow for faster transfer of our techniques and unlock novel applications, we actively seek to develop applications in the medical sector. In particular, we are involved in a project around the design of orthoses, which explores how our research on elasticity control through microstructure geometries can be specifically applied to the medical sector.
5 Social and environmental responsibility
5.1 Footprint of research activities
Our environmental footprint is limited. We use various products for 3D printing but in small quantities, and have put in place all required measures for recycling and disposal.
5.2 Impact of research results
We make our software IceSL freely available to the public and have continued this year to document its features, organize tutorials and demonstrations (e.g. at 3DPrint Paris), as well as animate our social media accounts. Through this, we hope to encourage adoption of our research and maximize its impact, in particular by encouraging its use within the maker communities.
A longer-term strategy of the team is to help develop potential uses of our technique in different fields. This is for instance a key motivation for our participation in the DORNELL challenge, which seeks to improve devices helping the mobility impaired.
The exploratory action AEX CONTINUA emphasizes applications using 3D printing technology to construct large-scale structures to safeguard marine habitats vulnerable to rising temperatures due to global warming. We have an ongoing collaboration with researchers of CNRS (Serge Planes) and ENS Ulm (Emmanuel Dormy) that seeks to tackle this particular problem in the case of coral reefs.
6 Highlights of the year
6.1 Awards
Camille Schreck was awarded the Young Research Fellow of Eurographics France (YRF EGFR) title in 2024.
7 New software, platforms, open data
7.1 New software
7.1.1 IceSL
-
Keyword:
Additive manufacturing
-
Scientific Description:
IceSL is the software developed within MFX, that serves as a research platform, a showcase of our research results, a test bed for comparisons and a vector of collaborations with both academic and industry partners. The software is freely available both as a desktop (Windows/Linux) and as an online version.
-
Functional Description:
IceSL allows users to model complex shapes through CSG boolean operations. Objects can be directly prepared and sent to a 3D printer for fabrication, without the need to compute an intermediate 3D mesh.
-
News of the Year:
IceSL's current stable version is 2.5.3. It has accumulated 178.5k downloads (stable/beta releases). Linux/Windows share of downloads is 31
% / 69 % respectively (no change from last year). The IceSL web portal gathers all useful resources (doc, download links, features, etc), as well as our online tools. The online slicer and printer are used, respectively, 34 and 14 times per day on average and the online modeler has been used 360 times since its inception on February 2024.Important milestones throughout the year for IceSL are, (1) pyicesl – python bindings of all slicing functionalities of IceSL, (2) webforge – a fully online subset of the modeling and slicing capabilities of IceSL, (3) curved slicing – a new component in IceSL that allows generating non planar slices that are optimal when printing geometry with particular features, and, (4) IceSL CI – a framework to automatically test the slicing capabilities of IceSL when the code base is updated/expanded.
- URL:
-
Contact:
Sylvain Lefebvre
7.1.2 Silice
-
Name:
Silice
-
Keywords:
FPGA, Programming
-
Functional Description:
Silice makes it possible to write algorithms for FPGAs in the same way we write them for processors: defining sequences of operations, subroutines that can be called, and using control flow statements such as while and break. At the same time, Silice lets you fully exploit the parallelism and niceties of FPGA architectures, describing operations and algorithms that run in parallel and are always active, as well as pipelines. Silice remains close to the hardware: nothing gets obfuscated away. When writing an algorithm you are in control of what happens at which clock cycle, with predictable rules for flow control. Clock domains are exposed. In fact, Silice compiles to and inter-operates with Verilog: you can directly instantiate and bind with existing modules.
-
Release Contributions:
2021 version.
-
News of the Year:
This year Silice continued to evolve, with an improved way to deal with constants in logic, as well as github actions to automate project builds (including fpga programming from a webpage). A dedicated framework was added to support synthesis for the ASIC pipeline of the TinyTapeout initiative. Several projects were submitted to be manufactured in TinyTapeout shuttles 7 and 8.
- URL:
-
Contact:
Sylvain Lefebvre
7.2 New platforms
Participants: Pierre-Alexandre Hugron, Salim Perchy, Vincent Belle, Lucas Ochocinski.
MFX continued its presence and participation within the Creativ'Lab, which is operated by Loria and funded by Inria, Loria, CNRS and Région Grand Est.
Non-planar printing For the purpose of correctly integrating curved printing in IceSL and performing extensive testing of this feature, Pierre-Alexandre Hugron has assembled a 3D printer with bed-rotation capabilities. This printer allows, via motors, to tilt the build plate in two different axes. By doing so, a curved (i.e., non-planar) deposition path can be printed more accurately and faster than a normal 3d printer.
Its firmware and parameter configuration had to be readapted to this specific goal and a kinematic model was constructed to correctly manage the build plate rotation motors. This allows IceSL to operate them in an agnostic way.
Maintenance and upgrades A series of maintenance operations were performed on the resin printers (e.g., change of VAT films, internal heater installation). Furthermore, all machines (filament, resin) were properly cared after (e.g., lubrication of axes, nozzle cleaning, adjusting belt tension, cleaning printing beds, firmware updates).
Our clay printer and laser cutter also had maintenance operations performed.
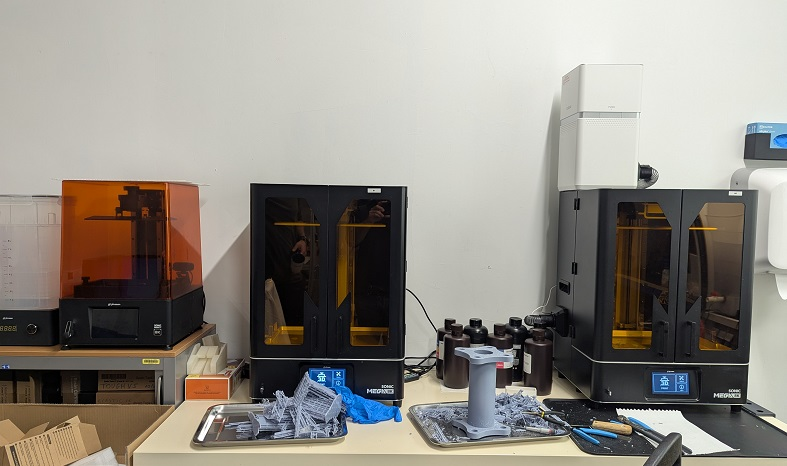
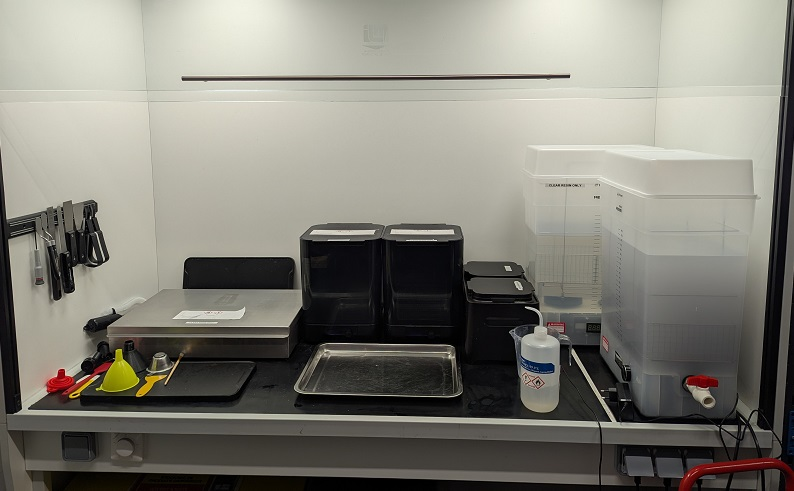
Resin printing room.
Resin printing room.
Work space safety We are continuously focusing on improving the safety of operation in the printing rooms. In 2024 Pierre-Alexandre Hugron and Salim Perchy followed three additional safety-oriented formations:
- Prévention à l'utilisation d'imprimantes 3d - CNRS Centre Est: Safety measures for different techniques of 3d printing (e.g., resin, filament, powder and metal)
- Habilitation Electrique pour des opérations simples ou d'ordre non électrique BS, BE - ERTF: Precautions and safety protocols when operating around low voltage machinery.
- Sauveteur et Secouriste du Travail (SST): Necessary skills for workplace accident prevention.
Several additional safety measures were put in place after these formations were attended:
- Particle sensors were placed in both printing rooms (filament and resin) that measure relevant information to prevent and detect degradation of air quality.
- Resin printers were equipped with air filters to avoid contamination of the room.
- Prevention signs were put up signaling required precautions and authorizations in all printing rooms.
- An exhaustive verification of all printers was conducted.
8 New results
8.1 StarDEM: efficient discrete element method for star-shaped particles
Participants: Camille Schreck, Sylvain Lefebvre, David Jourdan, Jonàs Martínez.
Granular materials composed of particles with complex shapes are challenging to simulate due to the high number of collisions between the particles. In this context, star shapes are promising: they cover a wide range of geometries from convex to concave and have interesting geometric properties. We proposed an efficient method to simulate a large number of identical star-shaped particles. Our method relies on an effective approximation of the contacts between particles that can handle complex shapes, including highly non-convex ones. We demonstrated our method by implementing it in a 2D simulation using the Discrete Element Method, both on the CPU and GPU.
This work was accepted at Eurographics short paper 17 and presented at Eurographics 2024. The code is available on github.

Three examples of simulation of 2D complex, non-convex, star-shaped particles.
8.2 Mesh Simplification For Unfolding
Participants: Manas Bhargava, Camille Schreck, Marco Freire, Pierre-Alexandre Hugron, Sylvain Lefebvre, Silvia Sellán, Bernd Bickel.
In collaboration with the Institute of Science and Technology Austria, we presented a computational approach for unfolding 3D shapes isometrically into the plane as a single patch without overlapping triangles. This is a hard, sometimes impossible, problem, which existing methods are forced to soften by allowing for map distortions or multiple patches. Instead, we propose a geometric relaxation of the problem: we modify the input shape until it admits an overlap-free unfolding. We achieve this by locally displacing vertices and collapsing edges, guided by the unfolding process. We validate our algorithm quantitatively and qualitatively on a large dataset of complex shapes and show its proficiency by fabricating real shapes from paper.
This work has been published in the journal Computer Graphics Forum (CGF) 14 and will be presented at Eurographics 2025. The code is available in github.
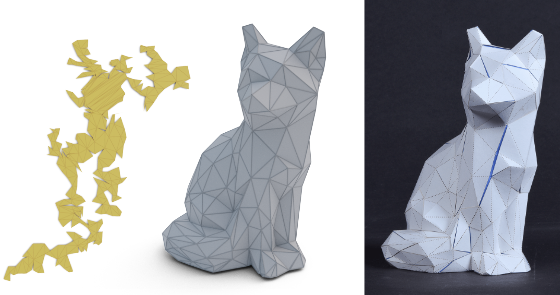
Computing a single-patch unfolding for an arbitrary input can be hard or outright impossible. Instead, we propose relaxing the problem and minimally modifying the input geometry to make it easily unfoldable. Our algorithm is robust and returns single-patch unfoldings for shapes of arbitrary genus and triangulation quality.
8.3 Anisotropic Specular Image-Based Lighting Based on BRDF Major Axis Sampling
Participants: Cédric Zanni, Giovanni Cocco, Xavier Chermain.
In the context of manufacturing, we are exploring ansisotropic appearances, both in terms of fabrication but also in terms of accurate previewing for modeling. Such anisotropic specular appearances are ubiquitous in the environment: brushed stainless steel pans, kettles, elevator walls, fur, or scratched plastics. Real-time rendering of these materials with image-based lighting is challenging due to the complex shape of the bidirectional reflectance distribution function (BRDF). We propose an anisotropic specular image-based lighting method that can serve as a drop-in replacement for the standard bent normal technique [Rev11]. Our method yields more realistic results with a 50% increase in computation time of the previous technique, using the same high dynamic range (HDR) pre-integrated environment image. We use several environment samples positioned along the major axis of the specular microfacet BRDF. We derive an analytic formula to determine the two closest and two farthest points from the reflected direction on an approximation of the BRDF confidence region boundary. The two farthest points define the BRDF major axis, while the two closest points are used to approximate the BRDF width. The environment level of detail is derived from the BRDF width and the distance between the samples. We extensively compare our method with the bent normal technique and the ground truth using the GGX specular BRDF.
This work was published in the journal Computer Graphics Forum 15 and presented at the conference Pacific Graphics 2024. The project page is here.
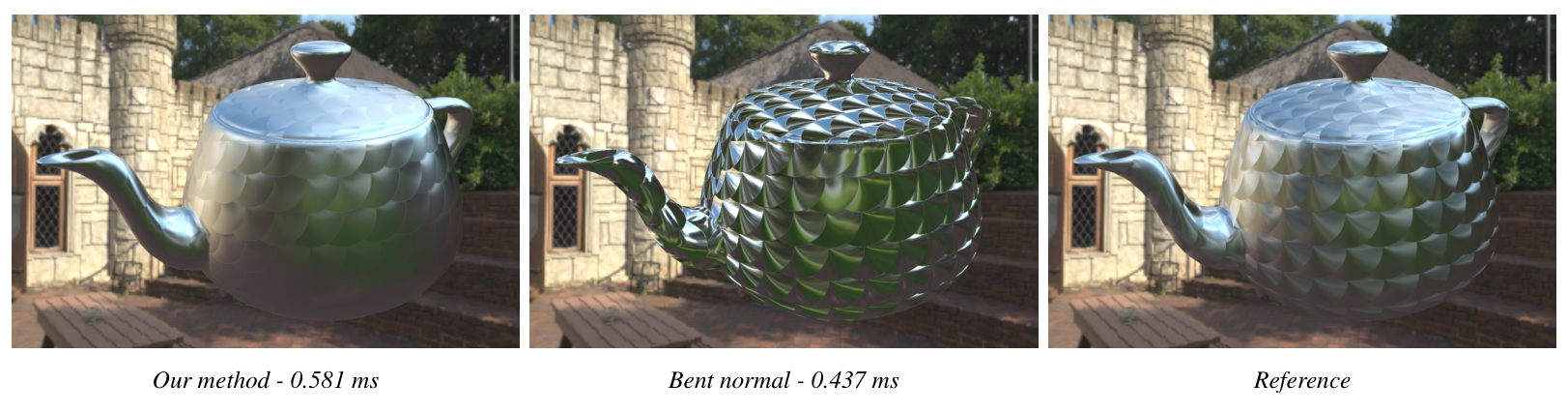
A circularly brushed metallic Utah teapot is rendered. The anisotropic specular material is illuminated through image-based lighting. From left to right: our method, the bent normal technique, and the reference image. Our technique uses 16 BRDF samples positioned along the major axis of the BRDF lobe, which improves the rendering quality compared to the bent normal technique that uses only one sample. Rendering times at a resolution of 1920 times 1080 with 8 times MSAA are provided below the images.
8.4 Synchronized Tracing of Primitive-based Implicit Volumes
Participants: Cédric Zanni.
Implicit volumes are known for their ability to represent smooth shapes of arbitrary topology thanks to hierarchical combinations of primitives using a structure called a blobtree. We present a new tile-based rendering pipeline well suited for modeling scenarios, i.e., no preprocessing is required when primitive parameters are updated. When using approximate signed distance fields (fields with Lipschitz bound close to 1), we rely on compact, smooth CSG operators - extended from standard bounded operators - to compute a tight augmented bounding volume for all primitives of the blobtree. The pipeline relies on a low-resolution A-buffer storing the primitives of interest of a given screen tile. The A-buffer is then used during ray processing to synchronize threads within a subfrustum. This allows coherent field evaluation within GPU workgroups. We use a sparse bottom-up tree traversal to prune the blobtree on-the-fly which allows us to decorrelate field evaluation complexity from the full blobtree size. The ray processing itself is done using the sphere tracing algorithm. The pipeline scales well to volumes consisting of thousands of primitives.
This work was published in the journal Transations on Graphics 16.
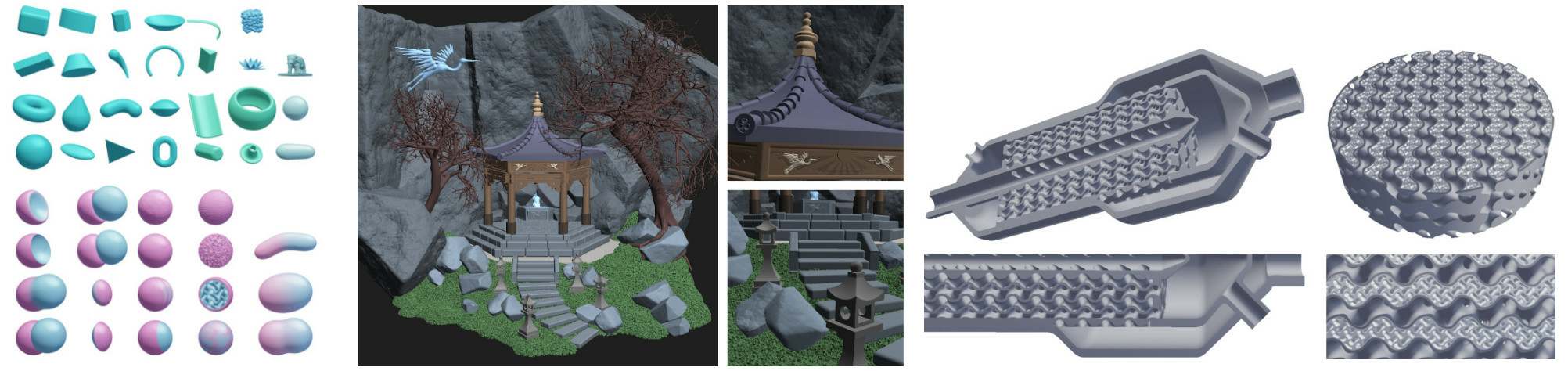
Overview of Forward inclusion functions for ray-tracing implicit surfaces
8.5 3D printed capacitive sensing
Participants: Jose Eduardo Aguilar-Segovia, Fabien Grzeskowiak, Maxime Manzano, Sylvain Guégan, Ronan Le Breton, Alice Farhi-Rivasseau, Sylvain Lefebvre, Marie Babel.
We explore augmenting parts with sensors fabricated in-situ, i.e. directly within the part, using functional materials deposited at the same time as the structural materials. However, achieving this goal at low cost remains challenging. This paper investigates the design of parametric capacitive sensors that can be embedded in complex designs. The sensors can be manufactured on multi-material extrusion 3D printers using commercially available non-conductive and conductive thermoplastic polyurethane.
The results of this project are published in the international journal IEEE Sensors12. This is joint work lead by the RAINBOW team, the LGCGM and the MFX team. This focuses on challenges relating to the PhD thesis of Eduardo Aguilar-Segovia and the DORNELL Inria challenge.
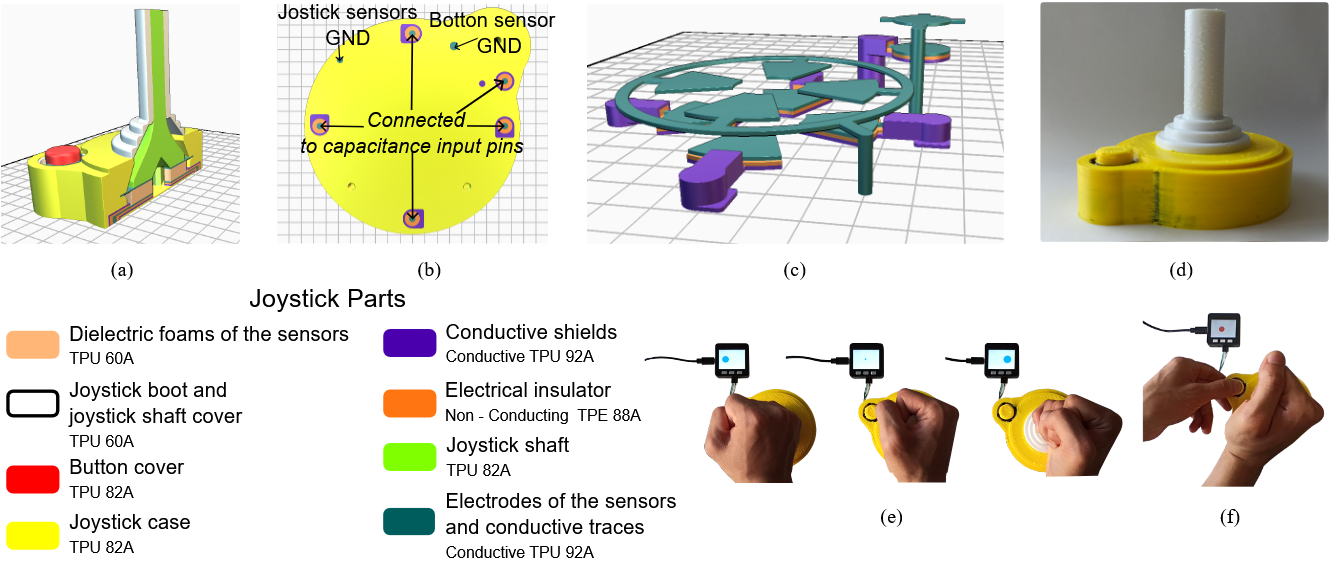
A functional joystick printed as a single multi-material part.
As an application of this methodology, we explored the fabrication of torque sensors. Measuring interaction forces between robots and humans is a major challenge in physical human-robot interactions. Nowadays, conventional force/torque sensors suffer from bulkiness, high cost, and stiffness, which limit their use in soft robotics. This work introduces a novel torque sensor manufactured with material extrusion technology. Our approach relies on capacitive structures, which are at the same time the deformable and the sensing parts of the sensor, making it very compact. These structures are made in one single multi-material print, simplifying the manufacturing process compared to traditional torque sensors.
The results of this project are published in the international journal IEEE Sensors Letters13. This is joint work lead by the RAINBOW team and the LGCGM, with ENS Rennes and the MFX team. This focuses on challenges relating to the PhD thesis of Eduardo Aguilar-Segovia and the DORNELL Inria challenge.
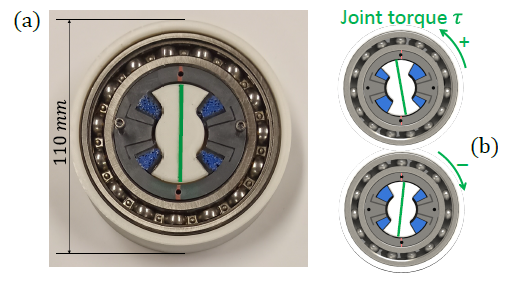
A torque sensor with a 3D printed inner core including capacitive, deformable sensors.
9 Bilateral contracts and grants with industry
9.1 Bilateral contracts with industry
Partnership with AddUp
Participants: Sylvain Lefebvre.
- Company: AddUp.
- Duration: Started in 2019.
- Abstract: AddUp is a French manufacturer of metal 3D printers for high-end industrial applications. We announced during FormNext 2019 (November) a partnership towards the creation of new software technologies. This partnership continued to develop in 2024.
Other industrial partnership
Participants: Sylvain Lefebvre.
- Company: S.A.M. Link
- Duration: Started in 2023.
- Abstract: The startup S.A.M. Signature Authentification des Matériaux develops additive manufacturing solutions for authentification, security and traceability. Sylvain Lefebvre is scientific advisor for the startup in the context of a technology transfer.
10 Partnerships and cooperations
10.1 International research visitors
10.1.1 Visits to international teams
Research stays abroad
In September 2024 (23-27), Jonàs Martínez, Eric Garner and Sylvain Lefebvre visited DTU (Danemark) during a week for discussions with Andreas Barentzen, Jeppe Revall Frisvad and Ole Sigmund. Jonàs and Sylvain gave a seminar at the Graphics Group.
10.2 European initiatives
10.2.1 Horizon Europe
KARST
KARST project on cordis.europa.eu
-
Title:
KARST: Predicting flow and transport in complex Karst systems
-
Duration:
From May 1, 2023 to April 30, 2029
-
Partners:
- INSTITUT NATIONAL DE RECHERCHE EN INFORMATIQUE ET AUTOMATIQUE (INRIA), France
- AGENCIA ESTATAL CONSEJO SUPERIOR DE INVESTIGACIONES CIENTIFICAS (CSIC), Spain
- UNIVERSITE DE NEUCHATEL (UNINE), Switzerland
- Simon Fraser University (SFU), Canada
- IFP Energies nouvelles (IFPEN), France
- UNIVERZA V LJUBLJANI (UL), Slovenia
-
Inria contact:
Sylvain Lefevre
- Coordinator:
-
Summary:
Karst aquifers are a treasure and a threat: while up to 25% of the world population depends on them for drinking water, they also have capabilities for extremely fast conduction of water and contaminants. In the light of climate change, we need to prepare for extreme flooding and understand the consequences for karst aquifers. Despite their socio-economic importance, decades of research, and high-profile disasters, karst structures and processes remain notoriously difficult to assess. Because of the complexity of karst and its lack of accessibility, the foundations of flow and transport modeling in karst systems are weak. Key phenomena related to extreme events such as flash floods and heavy tails in tracer recovery are still beyond current modeling capabilities.
KARST will establish the next generation of coupled stochastic modeling frameworks to predict karst processes, assess the vulnerability of karst aquifers, and forecast their response to extreme events. Our approach will bridge structures and processes on all scales, far beyond the capabilities of current theories and computer simulations. This will be achieved by targeting three key objec- tives: (i) Identification and quantification of flow and transport dynamics at the conduit scale. (ii) Characterization and modeling of karst network structure at the catchment scale. (iii) Derivation of a new upscaled approach to predict karst processes at different resolution scales. Together, this will result in an unprecedented multiscale modeling framework for the prediction of flow and transport in karst.
Solving this long-standing problem is possible thanks to the synergy of the KARST PI team combining the set of skills and knowledge (hydrogeology, physics, mathematics) required to make a ground-breaking step in this field. Beyond that, the new approach is expected to impact other real-world systems in medicine (capillary networks), neuroscience (brain microcirculation) or glaciology (meltwater flow in glaciers).
-
Activity in 2024:
In the context of the KARST project we designed and printed around 30 parts in different materials such as ABS for pipes, flexible 80A for seals and UltraClear resin for special optical parts, using around 20L of resin. This is an unprecedented level of production for the team, aiming at implementing the fluid testing installation assembled by the KARST team at IFPEN (Paris). Beyond modeling and printing, we work closely with the partners of the KARST project to design the novel experimental setup being built at IFPEN and resolve the challenges we encounter along the way. The printed parts are modular and can be rapidly adjusted to iterate as the installation is refined.
Two workshops were organized and attended for the purpose of project coordination, sharing of results and future work preparation. These workshops also provided context in many topics external to computer science (e.g., geology):
- 2nd Workshop KARST Ljubljana, Slovenia - 06-10 May, 2024.
- 3rd Workshop KARST Neuchatel, Switzerland - 13-17 November, 2024.
We hired Lucas Ochocinski to join the project on the design and additive manufacturing of parts.
3D printed parts on resin printers, KARST project.
Figure 8: 3D printed parts on resin printers, KARST project.
10.3 National initiatives
ANR ANISO
Participants: Xavier Chermain, Sylvain Lefebvre.
- Acronym: ANISO.
- Title: Anisotropic Appearance Fabrication With High-Resolution and Spatially Varying Orientations
- Duration: October 2024 – October 2028.
- Coordinator: Xavier Chermain.
- Abstract: Brushed finishes are widely used in architecture, large and small appliances, etc. ANISO aims to develop new digital and manufacturing technologies to produce customized and innovative anisotropic surface finishes. The aim is to go beyond unidirectional and circular surface finishes by allowing the designer to choose the brushing orientation for all surface positions. This freedom makes it possible to design customized and complex anisotropic appearances. Fabricating anisotropic appearances on 3D surfaces with arbitrary, spatially varying, high-definition orientations remains an open problem. We target glossy materials: metals (e.g., aluminum, silver, and gold), plastics (e.g., PETG and PLA), and glass. ANISO’s key idea is to use manufacturing processes that directly produce anisotropic surface roughness: Fused Filament Fabrication (FFF) and surface brushing. We plan to develop an algorithm that generates orientable, space-filling trajectories to control the direction of anisotropy at each point. Open-source software will be developed to interactively design and visualize anisotropic appearances with spatially variable directions to democratize the manufacture of this type of appearance. ANISO will enable Industry 4.0 to customize surface finishes and make them unique. Customization will be achieved using a single material that does not require paint or chemicals, making recycling easier. In addition, the surface finish of injection molding could be impacted by ANISO, enabling Industry 4.0 to produce customized parts and unique visuals on a large scale.
-
Activity in 2024:
As part of the ANISO project, we published an article on anisotropic appearance visualization 15 and presented it at the Pacific Graphics conference. Additionally, we hired Giovanni Cocco as a Ph.D. candidate in December 2024.
ANR MultiForm
Participants: Cédric Zanni.
- Acronym: MultiForm.
- Title: Multivariate Implicit Function defOrmation.
- Duration: 2023-2026.
- Coordinator: Loïc Barthe.
- Partners: Université Paul Sabatier, Ecole Polytechnique
- Abstract: This project aims at developing theoretical aspects of 3D field functions in computer graphics: 3D animation and the representation of complex multi-material virtual objects. An innovative aspect is the study of multivalued field functions and their deformations in this context. Practically, it aims at providing more efficient new solutions for both the deformation of animated 3D objects with collisions, and the representation of complex structures composed of several materials such as organic (muscular, bones, soft tissues) or liquid/solid structures (as a lava flow). The final goal being the deformations with collisions of these complex structures.
-
Activity in 2024:
Our latest results on efficient visualization of implicit surfaces has lead to a journal publication 16.
10.3.1 Inria
Inria Exploratory Action CONTINUA
Participants: Jonàs Martínez, Luis Mollericon.
- Acronym: AEx CONTINUA.
- Title: Continuous deposition of paste-like materials.
- Duration: 2022-2026.
- Coordinator: Jonàs Martínez.
- Abstract: Additive Manufacturing (AM) using paste-like materials such as clay or silicon enables the construction of large-scale structures but poses significant challenges for intricate geometries. During the manufacturing process, there is a heightened risk of structural collapse under gravity, leading to defects caused by repeated interruptions in extrusion flow. Previous efforts have primarily focused on simpler structures, failing to harness the full potential of AM. AEx CONTINUA aims to explore the realm of manufacturable deposition paths to empower the Additive Manufacturing of large-scale, complex structures, addressing the inherent challenges and pushing the boundaries of AM capabilities.
-
Activity in 2024:
Luis Mollericon Titirico visited DTU's mechanical engineering department this year from March to June to collaborate on a topology optimization research directly linked with this project. He was partially funded by the DrEAM fund of the Université de Lorraine.
Inria Challenge DORNELL
Participants: Sylvain Lefebvre, Pierre-Alexandre Hugron, Camille Schreck, David Jourdan, Vincent Belle.
- Acronym: DORNELL
- Title: A multimodal, shapeable haptic handle for mobility assistance of people with disabilities.
- Duration: 2022-2026.
- Coordinator: Marie Babel.
- Partners: Inria MFX, POTIOC,
- Abstract: While technology helps people to compensate for a broad set of mobility impairments, visual perception and/or cognitive deficiencies still significantly affect their ability to move safely and easily. DORNELL proposes an innovative multisensory, multimodal, smart haptic handle that can be easily plugged onto a wide range of mobility aids. Specifically fabricated to fit the needs of a person, it provides a wide set of tactile sensations in a portable and plug-and-play format – bringing haptics in assistive technologies all at once.
- Activity in 2024:
11 Dissemination
11.1 Promoting scientific activities
11.1.1 Scientific events: organisation
- Jonàs Martínez was organizer of the 1st Inria-CNRS Workshop on Physics and Computational Fabrication, Link.
11.1.2 Scientific events: selection
Chair of conference program committees
- Camille Schreck was co-chair of the Journées de l'AFIG 2024 best paper award (as YRF EGFR).
- Jonàs Martínez was program chair of the ACM Symposium on Computational Fabrication (SCF) held in Aarhus, Denmark.
- Sylvain Lefebvre was program co-chair of the Symposium on Geometry Processing (SGP), held at MIT, Cambridge (MA, USA).
Member of the conference program committees
- Camille Schreck was a member of the program committees of Eurographics short papers 2024, Symposium on Computer Animation (SCA) 2024, Pacific Graphics 2024, Siggraph Asia, poster and technical communication 2024 and Eurographics 2025.
- Xavier Chermain was a technical communications and posters committee member of SIGGRAPH Asia 2024.
- Cédric Zanni and Jonàs Martínez were program committee members of Journées Françaises d’Informatique Graphique (jFIG 2024)
- Sylvain Lefebvre was a member of the program committee of SIGGRAPH 2024 and Eurographics 2025.
Reviewer
- Camille Schreck was reviewer for Siggraph 2024.
- Xavier Chermain was a reviewer for SIGGRAPH, SIGGRAPH ASIA, SCF, UIST, PG.
- Cédric Zanni was a reviewer for Eurographics Short papers 2024.
- Jonàs Martínes was reviewer for Siggraph and Siggraph Asia 2024.
11.1.3 Journal
Reviewer - reviewing activities
- Cédric Zanni was a reviewer for Computer Graphics Forum, Computer-Aided Design.
11.1.4 Invited talks
- Camille Schreck gave an invited talk at the Journée de l'Afig (as YRF EGFR).
- Sylvain Lefebvre gave a keynote at the I3D 2024 conference, Philadelphia, USA. The talk is entitled The Gates of Graphics: A Deep Dive into Making Your Own Computer Graphics Hardware. Video
- Sylvain Lefebvre gave an invited talk at the first Graphics Programming Conference, in Breda (Netherlands), 2024. The talk is entitled From gates to pixels Video
- Sylvain Lefebvre gave a DCAMM seminar at DTU (Danemark) Link.
- Sylvain Lefebvre gave a seminar at ESPCI (January 26, 2024).
11.1.5 Leadership within the scientific community
- Jonàs Martínez was elected secretary of the executive board of the French chapter of Eurographics.
11.1.6 Scientific expertise
- Jonàs Martínez joined the evaluation committe of the Graphics Replicability Stamp Inititative.
11.1.7 Research administration
- Camille Schreck was invited member of the Eurographics France (EGFR) administrative board (as YRF EGFR).
- Camille Schreck was member of the center comittee of the Inria center of the Lorraine University.
- Sylvain Lefebvre is a member of the Bureau du Comité des Projets of the Inria center.
11.2 Teaching - Supervision - Juries
11.2.1 Teaching
- Master: Jonàs Martínez, Advanced machine architectures (GPU), 21h ETD, Télécom Nancy, France.
- Preparatory classes: Xavier Chermain, Nouveaux paradigmes de programmation et science des données, 64h ETD, prépa INP Nancy.
- Master: Camille Schreck, Introduction to 3D Graphics, 26h ETD, Telecom Nancy, France.
- Master: Camille Schreck, 3D Graphics and Parallelism, 12h ETD, ENSG Nancy, France.
- Master: Cédric Zanni, Software Engineering, 31.5h ETD, M1, École des Mines de Nancy, France.
- Master: Cédric Zanni, Introduction to C/C++, 54h ETD, M1, École des Mines de Nancy, France.
- Master: Cédric Zanni, C++ Programming, 31.5h ETD, M1, École des Mines de Nancy, France.
- Master: Cédric Zanni, Techniques for video game programming, 27h ETD, M1, École des Mines de Nancy, France.
- Master: Cédric Zanni, ARTEM Game Lab, 16h ETD, M1, École des Mines de Nancy, France.
- Master: Sylvain Lefebvre, Additive manufacturing for soft robotics, 6h ETD, École Polytechnique, Saclay, France.
- Master: Sylvain Lefebvre, Hardware design on FPGA, 12h ETD, Telecom Nancy, France.
- Master: Sylvain Lefebvre, Introduction to data parallelism with WebGPU, 30h ETD, Université de Lorraine, France.
- License: Cédric Zanni, Outils informatique, 12h ETD, L3, École des Mines de Nancy, France.
- License : Cédric Zanni, Introduction to Computer Science, 31.5h ETD, L3, École des Mines de Nancy, France.
- License: Pierre-Alexandre Hugron, Introduction to 3D printing, École des Mines, 6h ETD
- License: Marco Freire, Digital culture and tools, 17.3h ETD, Université de Lorraine, France
- License: Marco Freire, Programming projects, 57.3h ETD, Université de Lorraine, France
- Master: Marco Freire, Combinatorial optimization, 5.3h ETD, Université de Lorraine, France
- Label Éducation Supérieure: Marco Freire, Université de Lorraine, France
- License: Pierre-Alexandre Hugron, Introduction to modeling with IceSL. 12h ETD - IUT Charlemagne, France.
- University: Salim Perchy, Introduction to 3D printing with IceSL. 3h ETD - Universidad Javeriana, Cali - Colombia.
11.2.2 Supervision
- Research initiation: Aloïs Lemaux. The objectif is to create a pattern with surface water waves by optimizing the amplitude and phase of a set of fundemental sources. Advisor: Camille Schreck
- Internship – Antoine Ritter – Librairie C++ d'extraction de trajectoires cycliques – CESI engineering school – Advisors: Xavier Chermain and Sylvain Lefebvre – 15/01/2024 to 26/04/2024
- Internship – Giovanni Cocco – Anisotropic Specular Image-Based Lighting Based on BRDF Major Axis Sampling – University of Milan – Advisors: Xavier Chermain and Marco Tarini – 01/03/2024 to 30/08/2024
- Internship – Antoine Marion – Advisors: Xavier Chermain – 06/05/2024 to 14/06/2024 – GitHub
- Internship – Four high-school students – Advisors: Pierre-Alexandre Hugron and Xavier Chermain – 17/06/2024 to 18/06/2024
- Internship – Yan Rabefaniraka – Tool for automatization of printer profile creation in IceSL – Advisors: Salim Perchy and Pierre-Alexandre Hugron – 05/2024 to 06/2024 – GitHub
- Internship – Camille Charron – Clay printing with IceSL for Design School – Advisors: Pierre-Alexandre Hugron – 06/2024 to 07/2024
11.2.3 Juries
- Jonàs Martínez was member of the PhD. committe of David-Henri Garnier (École Polytechnique, France) and Riccardo Tonello (DTU, Denmark).
- Sylvain Lefebvre was reviewer (rapporteur) on the PhD committees of Emmanuel Rodriguez (Univeristy of Grenoble, France), Charline Grenier (University of Strasbourg, France), Rebekka Vaarum Woldseth (DTU, Danemark) and Peter Dorffler Ladegaard Jensen (DTU, Danemark). He presided the jury of Nariman Khaledia (Université de Lorraine, France). He was reviewer (rapporteur) for the Habilitation defense of Pooran Memari (École Polytechnique, France).
11.3 Popularization
11.3.1 Others science outreach relevant activities
- Café In' - February 22, 2024. Inria Nancy: Presentation on the ADT given to IceSL. The newest 3d printing features of IceSL were shown (e.g., optizor infill) as well as the recently introduced python bindings for IceSL (i.e., PyIceSL)
MFX Engineers Salim Perchy and Nathaniel Seyler demonstrating IceSL
Figure 9: Café In', Février 22, 2024 - IEEE-RAS International Conference on Humanoid Robots 2024 (Humanoids) - November 22-24 2024: Results and printed parts of MFX's research in additive manufacturing were shown and presented to the public and the French press.
Team leader Sylvain Lefebvre, Researcher Xavier Chermain and Research Engineer Pierre-Alexandre Hugron at MFX's stand during Humanoids 24
Figure 10: Humanoids 24, Novembre 22, 2024
12 Scientific production
12.1 Major publications
- 1 articleOptimal discrete slicing.ACM Transactions on Graphics361February 2017, 1 - 16HALDOI
- 2 articleFast ray tracing of scale-invariant integral surfaces.Computer Graphics Forum406September 2021, 117-134HALDOI
- 3 articleBridging the Gap: Automated Steady Scaffoldings for 3D Printing.ACM Transactions on Graphics334July 2014, 98:1 - 98:10HALDOI
- 4 articleCurviSlicer: Slightly curved slicing for 3-axis printers.ACM Transactions on Graphics384August 2019, 1–11HALDOI
- 5 articleVariable-width contouring for additive manufacturing.ACM Transactions on Graphics394 (Proc. SIGGRAPH)July 2020HALDOI
- 6 articleBy-example synthesis of structurally sound patterns.ACM Transactions on Graphics2015HALDOI
- 7 articleProcedural Voronoi Foams for Additive Manufacturing.ACM Transactions on Graphics352016, 1 - 12HALDOI
- 8 articleStructure and appearance optimization for controllable shape design.ACM Transactions on Graphics346November 2015, 12HALDOI
- 9 articlePolyhedral Voronoi diagrams for additive manufacturing.ACM Transactions on Graphics374August 2018, 15HALDOI
- 10 articleOrthotropic k-nearest foams for additive manufacturing.ACM Transactions on Graphics364July 2017, 121:1--121:12HALDOI
- 11 articleFreely orientable microstructures for designing deformable 3D prints.ACM Transactions on GraphicsDecember 2020HALDOI
12.2 Publications of the year
International journals
- 12 articleParametric Foam-Like Capacitive Sensors for 3D Printing of Deformable Parts with Sensing Capabilities.IEEE Sensors Journal2024, 1-1HALDOIback to textback to text
- 13 articleMulti-Material Torque Sensor Embedding One-Shot 3D-Printed Deformable Capacitive Structures.IEEE Sensors Letters89September 2024, 2503204HALDOIback to textback to textback to text
- 14 articleMesh Simplification for Unfolding.Computer Graphics ForumNovember 2024HALDOIback to text
- 15 articleAnisotropic Specular Image‐Based Lighting Based on BRDF Major Axis Sampling.Computer Graphics ForumOctober 2024. In press. HALDOIback to textback to text
- 16 articleSynchronized tracing of primitive-based implicit volumes.ACM Transactions on Graphics2024. In press. HALDOIback to textback to text
International peer-reviewed conferences
- 17 inproceedingsStarDEM: Efficient Discrete Element Method for Star-shaped Particles.EG 2024 - Short PapersEG 2024 EUROGRAPHICS ConferenceLimassol (Chypre), CyprusThe Eurographics Association2024HALDOIback to textback to text
Doctoral dissertations and habilitation theses
- 18 thesisLayout problems under topological constraints for computational fabrication.Université de LorraineJuly 2024HAL
Reports & preprints
- 19 miscPhasor-based dehomogenisation for microchannel cooling topology optimisation.December 2024HAL
Scientific popularization
- 20 inbookCAPTCH'YOU.THINK BEFORE LOADING2024HAL